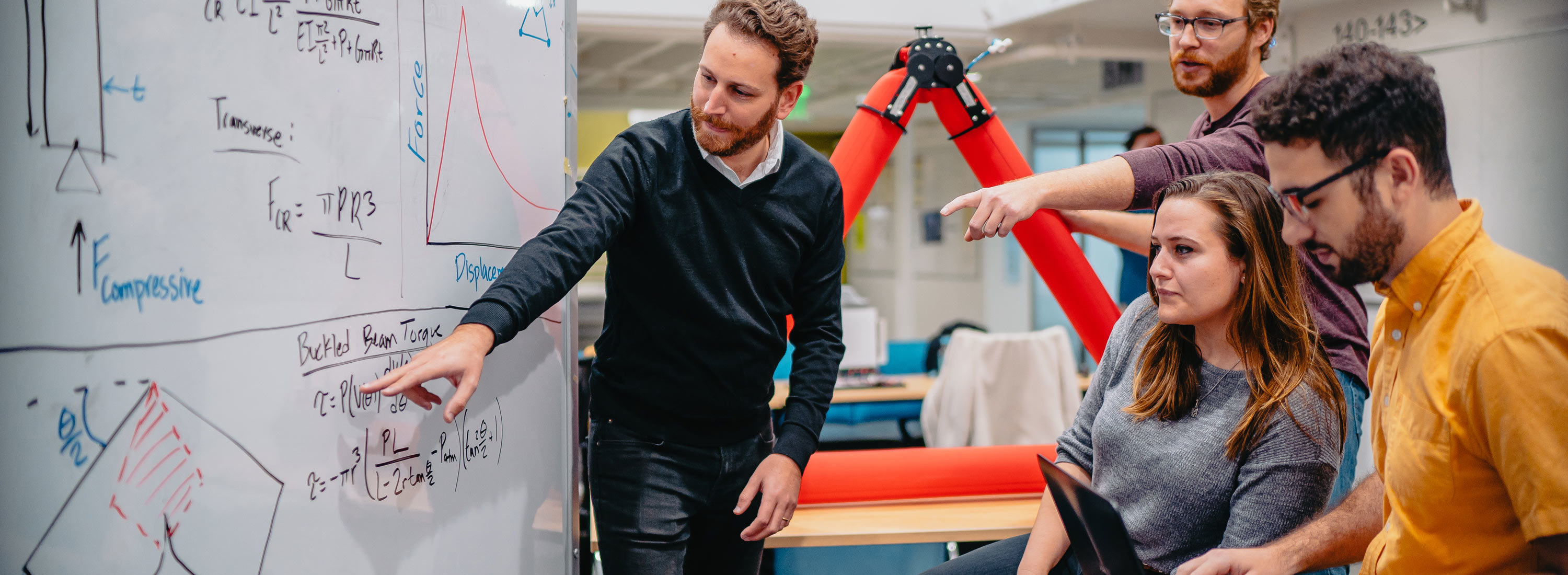
Mechanical engineering is one of the oldest and most versatile branches of engineering, encompassing everything from the design of spacecraft and prosthetic limbs to renewable energy systems and robotics. At its core, it blends scientific theory with hands-on innovation, using principles of physics, materials science, and mechanics to create systems that move, lift, power, and transform the world around us.
For high school students, especially those curious about how things work or passionate about designing solutions to everyday problems, mechanical engineering offers a powerful entry point into STEM. Unlike theoretical coursework, hands-on projects allow students to engage directly with the engineering process—conceptualizing an idea, building a prototype, testing it under real conditions, and refining it based on results.
Whether you’re building a bridge out of balsa wood, crafting a robotic arm, or experimenting with renewable energy, mechanical engineering projects encourage creative thinking, structured experimentation, and technical resilience—all of which are critical skills for college, careers, and lifelong learning.
These projects can serve multiple purposes:
- Prepare you for science fairs or engineering competitions
- Strengthen your college applications and research portfolios
- Help clarify your interest in pursuing mechanical engineering, robotics, or related disciplines
- Provide a foundation for more advanced innovation, like participating in patent-oriented or mentored research programs such as Nova Patent or Nova Research
Why Start in High School?
High school is the ideal time to explore engineering in a tangible way. By working on real projects, students not only learn technical concepts but also build confidence, discover their academic passions, and gain a deeper understanding of how engineers shape the world. These experiences also help students stand out when applying to selective universities or summer programs in engineering.
Even without access to a full machine shop or advanced fabrication tools, students can explore mechanical engineering principles using affordable, everyday materials. What matters most is your curiosity, creativity, and willingness to iterate—to test ideas, learn from failure, and improve your design with each step.
What This Guide Offers
In this article, we’ve curated 14 high-impact mechanical engineering project ideas that are suitable for high school students. These projects range from introductory builds like hydraulic arms and wind turbines to more complex prototypes like remote-controlled drones and electric vehicles. Each idea includes a brief explanation of:
- What the project involves
- What skills and concepts you’ll learn
- Ways to take the project further for competitions or research
Whether you’re exploring a personal passion, working on a team capstone project, or building your college portfolio, these ideas offer a launchpad for innovation. Some projects can even evolve into long-term research initiatives with real-world applications—especially when paired with mentorship or advanced learning programs.
So if you’re ready to take your first step into the world of mechanical engineering, this guide will help you turn your curiosity into creation.
1. Mini Wind Turbine
A mini wind turbine project is a compelling way to explore the principles of renewable energy and mechanical system design. In this project, you’ll construct a small wind-powered generator capable of converting kinetic energy from wind into electrical energy. It’s an ideal project for high school students interested in green energy, sustainability, or mechanical innovation.
Project Overview:
Build a small wind turbine using materials like PVC pipe, balsa wood, foam board, or 3D-printed components for the blades. Mount your turbine on a vertical or horizontal axis and connect it to a small motor or generator to produce electricity. Use a household fan or outdoor breeze to test different blade configurations and orientations.
Key Learning Objectives:
- Aerodynamics: Understand how blade shape, pitch, and number influence airflow and rotational speed.
- Mechanical torque: Explore how rotational force translates into usable power.
- Energy conversion: Learn how mechanical energy is transformed into electrical energy using a generator or DC motor.
- Design optimization: Test variables like blade length, material stiffness, or hub height to maximize output.
Real-World Applications:
This project mirrors the engineering challenges involved in scaling wind farms, especially for remote or off-grid regions. It introduces students to topics central to sustainable energy systems, climate solutions, and infrastructure design.
Advanced Add-Ons:
- Use an Arduino or Raspberry Pi to measure voltage, current, and power output in real time.
- Create a data logging system to compare turbine efficiency under different wind conditions or blade types.
- Design a dual-axis tracking system that adjusts turbine orientation to face optimal airflow (mimicking real-world yaw control systems).
College Portfolio Tip:
Document your design iterations, testing data, and engineering process in a digital portfolio. If applying to STEM programs, especially those focused on environmental engineering, mechanical systems, or renewable energy, this project can showcase your initiative and technical curiosity.
2. Hydraulic Arm
A hydraulic robotic arm is a classic mechanical engineering project that offers an exciting introduction to fluid mechanics and motion control. By using water-filled syringes and tubing to manipulate joints, students can simulate the movement of real-world hydraulic systems—like those used in construction equipment, prosthetics, or industrial automation.
Project Overview:
In this project, you’ll build a multi-jointed arm using syringes as actuators, plastic tubing to carry water, and lightweight materials like cardboard, wood, or acrylic for the structural frame. By adjusting fluid pressure manually, the syringes extend or retract to move parts of the arm—mimicking muscles and joints.
Test your design by having the arm pick up, move, or stack small objects such as blocks, ping-pong balls, or cups.
Key Learning Objectives:
- Pascal’s Law: Understand how pressure applied to a confined fluid is transmitted equally in all directions, a fundamental concept in fluid power systems.
- Mechanical linkages and control: Explore how levers and pivot points convert linear force into rotational motion.
- Precision and articulation: Practice designing joints that mimic real human arm movement, including shoulder, elbow, and wrist motion.
- System balance: Learn how to evenly distribute force and ensure smooth motion without overextending hydraulic lines.
Real-World Applications:
This project mirrors technologies used in robotics, prosthetic design, and heavy machinery. From backhoes to robotic arms in surgical systems, hydraulic control is essential in fields where strength, precision, and reliability are key.
Advanced Add-Ons:
- Add wrist articulation or finger movement using additional syringes and tubing to increase degrees of freedom.
- Design a joystick-style controller to operate the arm remotely, simulating the interface of professional robotic systems.
- Experiment with different fluid types or tube diameters to observe changes in speed and force transmission.
- Build a vertical arm with multiple axes and compare performance to simpler single-plane designs.
College Portfolio Tip:
Include sketches, photos, and video documentation of your arm in action. Use a design log to reflect on challenges like fluid leaks or movement calibration. This kind of documentation is especially compelling for college applications in mechanical, biomedical, or robotics engineering—demonstrating both hands-on skill and design thinking.
3. Pneumatic Can Crusher
A pneumatic can crusher is a high-impact project that introduces students to compressed air systems and automation technology. This project simulates the kinds of pneumatic actuators used in factory assembly lines and industrial robotics—offering a strong foundation in mechanical automation and systems engineering.
Project Overview:
In this project, you’ll design a system that uses compressed air to activate a piston or ram that crushes aluminum soda cans. The structure can be made from wood, metal, or acrylic, and the pneumatic force is generated using an air compressor or a high-pressure pump.
Test the system’s strength and cycle efficiency by crushing multiple cans in succession, and refine your design to increase stability, force distribution, and safety.
Key Learning Objectives:
- Air pressure and force multiplication: Learn how compressing air stores energy that can be released to do mechanical work.
- Mechanical leverage: Explore how to direct and amplify pneumatic force using linkages and leverage systems.
- System design and safety: Understand how to incorporate valves, actuators, and structural supports in an integrated mechanical system.
Real-World Applications:
Pneumatic systems are used in countless industries—from automated manufacturing and car assembly to medical devices and robotics. This project demonstrates how air-powered systems offer a clean, efficient alternative to hydraulics in certain applications.
Advanced Add-Ons:
- Integrate a foot pedal or push-button valve for hands-free operation and quicker cycling.
- Add a programmable timer or sensor to activate the system automatically after a delay or trigger event.
- Explore safety interlocks or emergency stop mechanisms, mirroring industrial standards.
College Portfolio Tip:
Document how you tested air pressure, structural integrity, and control precision. Include technical drawings and safety precautions in your engineering notebook. If you're interested in industrial design, automation, or mechanical systems, this project shows a clear connection to real-world engineering applications.
4. Robotic Hand
A robotic hand is a powerful interdisciplinary project that brings together elements of mechanical engineering, electronics, and biomedical design. This project challenges students to replicate the complexity of human hand movements using actuators, linkages, and sensors.
Project Overview:
Using servos, strings (to simulate tendons), and lightweight materials like plastic or foam board, you’ll build a robotic hand capable of gripping or flexing. Movement can be controlled via Arduino, Raspberry Pi, or analog switches. Enhance the realism by designing joints that mimic knuckles and phalanges.
Test the hand by picking up small objects or performing gesture-based tasks like a thumbs-up or sign language alphabet.
Key Learning Objectives:
- Biomechanics and anatomy: Understand how tendons, joints, and muscle groups work together to enable dexterous movement.
- Servo actuation and control systems: Learn how to program microcontrollers to control motor movement in response to user inputs.
- Sensor integration: Use flex sensors, pressure sensors, or myoelectric inputs to simulate more advanced prosthetic control.
Real-World Applications:
Robotic hands are used in fields like prosthetics, assistive technology, robotic surgery, and industrial automation. Students exploring biomedical or mechanical engineering will gain insight into both functional design and human-centered applications.
Advanced Add-Ons:
- Integrate flex sensors or EMG electrodes to mimic movement based on actual muscle input.
- Use gesture recognition or machine learning to allow the hand to respond to visual or sensor-based cues.
- Add adaptive grip strength to hold objects of different weights and shapes.
Interdisciplinary Focus:
This project is especially valuable for students interested in the intersection of technology, healthcare, and robotics. It can also serve as a springboard into biomedical research or prosthetic innovation.
College Portfolio Tip:
Showcase the evolution of your design—from sketches and prototypes to final assembly. Include code snippets, component lists, and reflections on how your hand models the complexity of human anatomy. This is an excellent capstone project for students pursuing biomedical, mechanical, or mechatronic engineering.
5. Solar Oven
A solar-powered oven is a simple yet powerful project that introduces students to renewable energy and heat transfer concepts. This hands-on design challenge helps you explore how to harness solar radiation to cook food—while optimizing for efficiency, sustainability, and real-world application.
Project Overview:
Design a functional oven using cardboard, aluminum foil, glass or clear plastic, and insulating materials like foam or wool. The oven collects sunlight, reflects and concentrates it toward a cooking chamber, and retains heat through insulation. You’ll track internal temperatures with a thermometer and test how quickly different items (like s’mores, toast, or rice) cook under various conditions.
Key Learning Objectives:
- Thermodynamics: Learn how heat is transferred via radiation, conduction, and convection.
- Solar energy collection: Explore how reflective materials and angle adjustment can intensify heat concentration.
- Sustainable engineering: Understand how low-cost, passive solar systems can be used in off-grid or low-resource environments.
Real-World Applications:
Solar ovens are used globally in regions with limited access to electricity or fuel, supporting sustainable cooking and water pasteurization. This project connects engineering with public health, environmental science, and humanitarian design.
Advanced Add-Ons:
- Test how different reflector angles, colors, or materials affect heating efficiency.
- Design a solar tracking mechanism that adjusts panel angles for maximum sun exposure throughout the day.
- Compare insulation methods (cotton, mylar, fiberglass) for heat retention.
- Log and graph cooking temperatures over time for different food types or weather conditions.
College Portfolio Tip:
Include photos of your oven in action, time-lapse cooking data, and written analysis of your design choices. If you're applying to programs in environmental engineering, physics, or sustainable design, this project highlights initiative and real-world relevance.
6. Hovercraft
A hovercraft project is an exciting introduction to fluid mechanics, air pressure, and mechanical propulsion. This STEM challenge gives students a firsthand look at how engineers reduce friction to create smooth, low-resistance motion across surfaces.
Project Overview:
Construct a small hovercraft using lightweight materials like foam board or CDs, powered by a balloon, small fan, or motor. Air is pushed beneath the platform to form a cushion between the base and the ground, allowing the hovercraft to float and glide. The goal is to minimize friction and maximize distance or stability.
Key Learning Objectives:
- Fluid dynamics and pressure: Understand how trapped air beneath a platform can reduce contact friction.
- Propulsion and lift: Explore how varying airflow impacts stability, speed, and balance.
- Friction and motion: Apply Newton’s laws to analyze movement with minimal resistance.
Real-World Applications:
Hovercraft technology is used in search-and-rescue missions, amphibious military transport, and high-speed ferries. This project gives students insight into the engineering of vehicles that traverse land, water, and ice.
Advanced Add-Ons:
- Replace the balloon with a motorized fan for consistent propulsion and test different airflow outputs.
- Add a rudder or directional control system to steer the craft more precisely.
- Test performance on different surfaces: hardwood, carpet, sandpaper, or ice.
- Experiment with platform shape and size to determine which offers the best lift-to-weight ratio.
College Portfolio Tip:
Show how you iterated on design for improved performance—include velocity measurements, surface comparisons, and airflow calculations. This project is particularly valuable for students interested in aerospace, fluid mechanics, or transportation engineering.
7. Mechanical Clock
Designing a mechanical timekeeping device introduces students to the delicate balance of precision engineering and dynamic motion control. This project combines mechanical creativity with analytical thinking, as students replicate the inner workings of clocks that have stood the test of time.
Project Overview:
Build a functioning clock using gears, escapements, weights or springs, and a pendulum or balance wheel. The aim is to create a mechanism that moves steadily and consistently, translating energy into accurate, timed rotation of clock hands.
You can use wood, acrylic, or 3D-printed parts to craft your own gear system and explore how each element interacts to maintain consistent timing.
Key Learning Objectives:
- Gear ratios: Learn how gear trains reduce or increase speed, and how they maintain synchronization between components.
- Escapement mechanisms: Understand how energy is regulated and released at precise intervals in traditional clocks.
- Rotational dynamics: Explore torque, angular momentum, and how mass distribution affects timekeeping.
Real-World Applications:
This project reflects principles used in watchmaking, robotics, mechanical automation, and timing systems in engineering and computing. Understanding mechanical timing is also foundational to fields like mechatronics and aerospace engineering.
Research Component:
- Study the history of chronometry, from ancient sundials to atomic clocks.
- Explore the transition from mechanical to digital systems in modern engineering.
Advanced Add-Ons:
- Incorporate a winding system for energy storage using springs or hanging weights.
- Design a transparent gear system for visual appeal and instructional use.
- Add a chime or alarm mechanism for functional interaction.
College Portfolio Tip:
Photograph your build at each stage, and annotate your sketches to show how precision, weight balance, and mechanical tolerances influenced your design. This project demonstrates both technical ability and attention to detail—ideal for students applying to mechanical, aerospace, or precision engineering programs.
8. Water Rocket Launcher
A water rocket launcher is a thrilling and educational way to engage with physics, aerodynamics, and design iteration. It’s a favorite for science fairs and competitions, combining explosive fun with deep learning about thrust, trajectory, and Newtonian mechanics.
Project Overview:
Construct a launcher that uses air pressure and water to propel a plastic bottle rocket into the air. The system typically includes a base for stability, a locking mechanism, and a pressure input (like a bike pump). Adjust water volume, launch angle, and air pressure to optimize distance and height.
Key Learning Objectives:
- Projectile motion: Understand how velocity, angle, and gravity affect trajectory.
- Thrust and pressure: Explore Newton’s third law—every action has an equal and opposite reaction.
- Experimental testing: Use trial and error to test different fin designs, bottle shapes, and launch variables.
Real-World Applications:
This project mirrors basic concepts used in rocket propulsion, aerospace design, and fluid dynamics. It’s an entry point for students interested in engineering fields that involve launch systems, aerodynamics, or mechanical testing.
Data Collection:
- Use a video camera or smartphone to analyze launch footage in slow motion.
- Measure altitude with a barometric altimeter, drone, or trigonometric method using an observer and protractor.
Advanced Add-Ons:
- Build a multi-stage rocket with parachute recovery.
- Integrate a remote-controlled valve release or countdown timer.
- Test different nozzle sizes and fin configurations for stability and efficiency.
College Portfolio Tip:
Include launch diagrams, pressure logs, and design evolution. Pair this project with a written reflection on engineering process and iterative design. Great for students interested in aerospace engineering, mechanical design, or applied physics.
9. Magnetic Levitation Train
A magnetic levitation (maglev) train model is a futuristic and visually stunning project that demonstrates principles of electromagnetism, stability, and low-friction transport. This project introduces advanced mechanical and electrical concepts in a format that’s tangible and rewarding.
Project Overview:
Design a small-scale maglev track and train using repelling magnets or electromagnetic coils to lift and propel the train. The train floats above the track, reducing friction and enabling smooth, fast motion. You can build a linear guideway using wood or foam board and embed magnets or copper wire to generate magnetic force.
Key Learning Objectives:
- Magnetic fields: Learn how like poles repel and how magnetic orientation affects lift and stability.
- Electromagnetic force: Understand how coils and current can create controlled magnetic movement.
- Frictionless transportation: Analyze how removing physical contact improves energy efficiency and speed.
Real-World Applications:
This project simulates the technology used in real-world maglev trains in Japan, China, and Germany, which travel at speeds over 300 mph using advanced electromagnetic systems. It ties into careers in transportation engineering, electromagnetics, and urban infrastructure design.
Advanced Upgrades:
- Add Hall effect sensors or photodiodes to detect train position and control acceleration.
- Integrate a linear induction motor or solenoid coils for propulsion without wheels.
- Create a feedback control system to adjust levitation height dynamically.
College Portfolio Tip:
Document each stage of your design process—from magnet placement tests to motion stability evaluations. Use simulations or field mapping to explain how magnetic forces interact. This project demonstrates advanced thinking and is excellent for students pursuing electrical engineering, transportation systems, or applied physics.
10. Kinetic Sculpture
A kinetic sculpture combines artistic expression with the principles of motion and mechanics. It’s a perfect project for students who enjoy blending visual creativity with engineering design, offering an engaging way to explore how mechanical systems can create movement in response to environmental forces.
Project Overview:
Design and build a sculpture that moves using wind, gravity, touch, or motor-driven components. Your piece might include gears that turn with the breeze, cams that create rhythmic movement, or counterweights that initiate a slow descent. Materials can include wood, metal, wire, 3D-printed parts, or repurposed everyday objects.
Focus on creating a balance between form and function—your sculpture should be both visually compelling and mechanically sound.
Key Learning Objectives:
- Mechanical motion transfer: Understand how forces are transmitted through gears, cams, cranks, and levers.
- Design thinking: Learn how to integrate aesthetics with physics, creating a visually pleasing yet functional piece.
- Balance and stability: Explore how structure, weight, and counterforces impact motion.
Real-World Applications:
Kinetic art is used in architecture, product design, animation, and interactive installations. This project is ideal for students interested in STEAM (science, technology, engineering, arts, and math) careers such as industrial design or mechanical sculpture.
Advanced Add-Ons:
- Incorporate solar panels or small motors for powered motion.
- Add microcontrollers (Arduino) to respond to environmental triggers like light, temperature, or motion.
- Design a modular piece where parts move independently and affect one another.
College Portfolio Tip:
Showcase both your creative process and engineering approach. Include sketches, material selection rationale, mechanical schematics, and time-lapse photos or video. This project is particularly powerful for applications to design, mechanical engineering, or architecture programs.
11. Electric Go-Kart
Building an electric go-kart is an ambitious and rewarding project that introduces students to vehicle dynamics, electric power systems, and mechanical design. It’s a real-world application of engineering principles that delivers excitement and educational depth.
Project Overview:
Construct a small electric vehicle using a chassis (metal or wood), DC motors or brushless motors, batteries, wheels, and a throttle control system. Test how weight distribution, gearing ratios, and motor selection affect speed, torque, and battery life. Safety is crucial—include proper braking and ensure adult supervision and controlled environments during testing.
Key Learning Objectives:
- Power systems and batteries: Learn how electrical energy is stored and transferred through motor systems.
- Transmission and gearing: Explore how torque and speed are influenced by gear ratios and drivetrain design.
- Mechanical integration: Understand how all subsystems—frame, drive, brakes, and steering—must work in harmony.
Real-World Applications:
This project is a scaled-down introduction to automotive, mechanical, and electrical engineering. It mirrors the challenges engineers face in designing electric vehicles (EVs), making it ideal for students interested in sustainability, mobility, or innovation.
Advanced Add-Ons:
- Add regenerative braking or a digital display showing battery stats.
- Use Arduino or Raspberry Pi to log performance data like speed, temperature, or current draw.
- Explore chassis aerodynamics or suspension for improved handling.
College Portfolio Tip:
This project can become a showstopper in your application. Include CAD drawings, wiring diagrams, performance tests, and safety protocols. It’s ideal for aspiring engineers focused on automotive systems, mechatronics, or robotics.
12. Water Filtration System
Designing a water filtration system is a meaningful and hands-on way to explore environmental engineering, fluid dynamics, and public health. It empowers students to apply engineering principles to one of the world’s most pressing challenges: access to clean water.
Project Overview:
Build a water filtration prototype using layers of common filtration materials like sand, gravel, charcoal, cotton, and activated carbon. Water can be moved through the system using gravity, hand pumps, or basic pressure systems. Collect and analyze filtered water to assess effectiveness based on clarity, smell, and pH.
This project is scalable—from tabletop designs to field-ready filters for emergency response or developing regions.
Key Learning Objectives:
- Environmental chemistry: Learn how physical and chemical filters remove contaminants and improve water quality.
- Pressure systems and flow: Explore how water moves through layers and how pressure affects filtration speed and efficiency.
- Testing and optimization: Use scientific methods to assess purification quality and iterate designs accordingly.
Real-World Applications:
Water filtration is central to global health, humanitarian engineering, and sustainability. This project ties directly to careers in civil engineering, environmental science, and public policy.
Test and Iterate:
- Use turbidity tubes, test strips, or pH kits to evaluate filtered water.
- Compare different configurations (e.g., vertical gravity-fed vs. pressurized).
- Test how flow rate affects filtration effectiveness and contaminant removal.
Advanced Add-Ons:
- Add UV purification using LEDs or solar-based disinfection methods.
- Create a modular system for different types of contaminants (sediment, metals, bacteria).
- Develop a portable version for use in disaster zones or off-grid environments.
College Portfolio Tip:
Highlight the global relevance of this project. Pair it with research on real-world applications and humanitarian case studies. It’s an excellent fit for students applying to programs in environmental engineering, global health, or sustainability.
13. Remote-Controlled Drone
Building a remote-controlled quadcopter is an immersive and technically advanced project that gives students hands-on experience with aerodynamics, flight mechanics, and electronic control systems. As drones continue to revolutionize industries—from logistics and cinematography to agriculture and defense—this project offers both fun and future-forward learning.
Project Overview:
Assemble a quadcopter using motors, ESCs (electronic speed controllers), a flight controller, battery pack, and transmitter/receiver. You can use a ready-to-assemble drone kit or source components individually to create a customized build. Once assembled, calibrate your drone and test flight stability, control response, and lift capacity.
Experiment with different frame materials, propeller sizes, and battery weights to assess how each factor impacts lift, maneuverability, and flight time.
Key Learning Objectives:
- Aerodynamics and thrust: Learn how propeller design and motor power generate lift and influence flight stability.
- Electronic systems integration: Understand how controllers, sensors, and power systems coordinate to enable precise flight.
- Flight tuning and control logic: Adjust settings like PID values to improve responsiveness and reduce wobble.
Real-World Applications:
This project mirrors the systems used in real-world unmanned aerial vehicles (UAVs) for delivery, mapping, surveillance, and emergency response. It also introduces concepts used in robotics, aerospace engineering, and autonomous systems.
Advanced Add-Ons:
- Integrate GPS modules for navigation and autonomous flight paths.
- Add ultrasonic or infrared sensors for obstacle avoidance.
- Install an FPV (first-person view) camera to simulate commercial drone piloting.
- Program flight logic using platforms like Betaflight or Arduino for custom control features.
College Portfolio Tip:
Document the full build—from soldering components and testing power output to flight trials and upgrades. This project showcases advanced problem-solving and interdisciplinary knowledge—ideal for applications in aerospace, robotics, mechatronics, or electrical engineering.
14. DIY 3D Printer
Building a DIY 3D printer combines the mechanical precision of traditional engineering with the innovation of additive manufacturing. This project offers an in-depth look at how hardware, software, and material science come together to turn digital designs into physical objects—making it one of the most versatile engineering builds for students.
Project Overview:
Start by assembling a 3D printer from a kit (such as Prusa, Creality, or Anycubic) or go further by designing a custom machine using open-source parts, including stepper motors, linear rails, extruders, a control board (e.g., RAMPS or Duet), and firmware like Marlin.
Once assembled, calibrate the printer, tune its motion settings, and experiment with CAD software to design and print custom models—anything from spare parts and engineering tools to prototypes for other mechanical projects.
Key Learning Objectives:
- Stepper motor control: Learn how motion systems translate software commands into precise physical movements.
- CAD/CAM integration: Use tools like Fusion 360, TinkerCAD, or SolidWorks to design printable models.
- Additive manufacturing fundamentals: Understand filament behavior, layer adhesion, extrusion mechanics, and temperature control.
Real-World Applications:
3D printing is central to product design, medical prototyping, architecture, and manufacturing innovation. Mastery of this technology gives students a head start in mechanical design, industrial engineering, or rapid prototyping careers.
Advanced Add-Ons:
- Upgrade with a dual extruder for multi-material or multi-color printing.
- Add automatic bed leveling, filament sensors, or enclosure systems for improved reliability.
- Explore resin printing or SLA methods for finer resolution models.
- Print custom parts to enhance other mechanical engineering projects (e.g., drone frames, gearboxes, prosthetics).
College Portfolio Tip:
Include detailed build logs, test prints, calibration processes, and design-to-print workflows. Bonus: if you use your printer to create parts for other research or engineering projects, document that integration to highlight your engineering versatility and innovation.
Making the Most of Your Mechanical Engineering Project
Building a mechanical engineering project is more than a classroom exercise—it can be the foundation for a transformative academic journey. By documenting, iterating, and expanding your project thoughtfully, you can turn a hands-on build into a research portfolio, college application standout, or competition-ready innovation.
Extend Your Project’s Impact
High school students who go beyond the build phase often find their work leading to prestigious opportunities in:
- Science fairs and innovation challenges
Competitions such as the Regeneron International Science and Engineering Fair (ISEF), Conrad Challenge, or VEX Robotics are ideal platforms to present well-documented projects. Judges and reviewers look for originality, data analysis, iterative design, and real-world relevance—all skills honed through in-depth mechanical builds. - College applications and essays
Admissions officers are increasingly drawn to students who demonstrate initiative, intellectual curiosity, and creative problem-solving. A project that begins as a hobby can evolve into a compelling story of growth, especially when students reflect on challenges, breakthroughs, and their evolving interest in STEM. - Mentored research and innovation programs
Turning your project into an original contribution to a field—whether it's sustainable design, robotics, or transportation—often requires expert guidance. Programs like Nova Research and Nova Patent offer high school students the opportunity to do just that.
How Nova Scholar Programs Can Support You
Nova Scholar Education’s Nova Research (2.5–5 months) and Nova Patent (2–4 months) programs pair ambitious students with PhD mentors from Stanford, MIT, Harvard, Yale, and Princeton. These mentors guide students in:
- Refining project design with research methodology
- Exploring deeper technical or interdisciplinary questions
- Preparing portfolios, prototypes, or patent applications
- Writing high-level research papers or innovation briefs
This kind of mentorship helps students take their mechanical engineering projects from exploratory builds to college-ready research portfolios—especially important for students aiming at top-tier STEM programs.
Beyond AP Classes: Showing Depth and Initiative
While AP Physics, AP Calculus, and other coursework show academic rigor, independently designed engineering projects reveal qualities that college admissions committees actively seek:
- Curiosity: Are you driven to explore beyond the curriculum?
- Persistence: How do you handle design flaws and failed prototypes?
- Vision: Can you see the real-world impact of your idea?
Documenting your progress—from sketches and CAD models to field tests and data analysis—not only helps you refine your work but also builds the foundation for research abstracts, project websites, or digital portfolios.
Final Thoughts
Whether you're experimenting with solar energy, testing the laws of motion, or exploring robotics, mechanical engineering projects offer a window into real-world innovation. They combine technical theory with hands-on creation and allow students to see the tangible impact of engineering solutions.
Choosing a project that aligns with your interests—whether it's energy, transportation, robotics, or sustainability—can not only deepen your understanding but also help you envision how engineering shapes the world around us.
Start with curiosity. Build with intention. Learn by doing.
If you're ready to take your project further, consider seeking mentorship, entering competitions, or conducting research that could one day lead to real-world applications—or even a patent.
Let your first engineering build be the beginning of a bigger journey.